Fume Cupboard Testing in Newport: Ensuring Safety and Efficiency
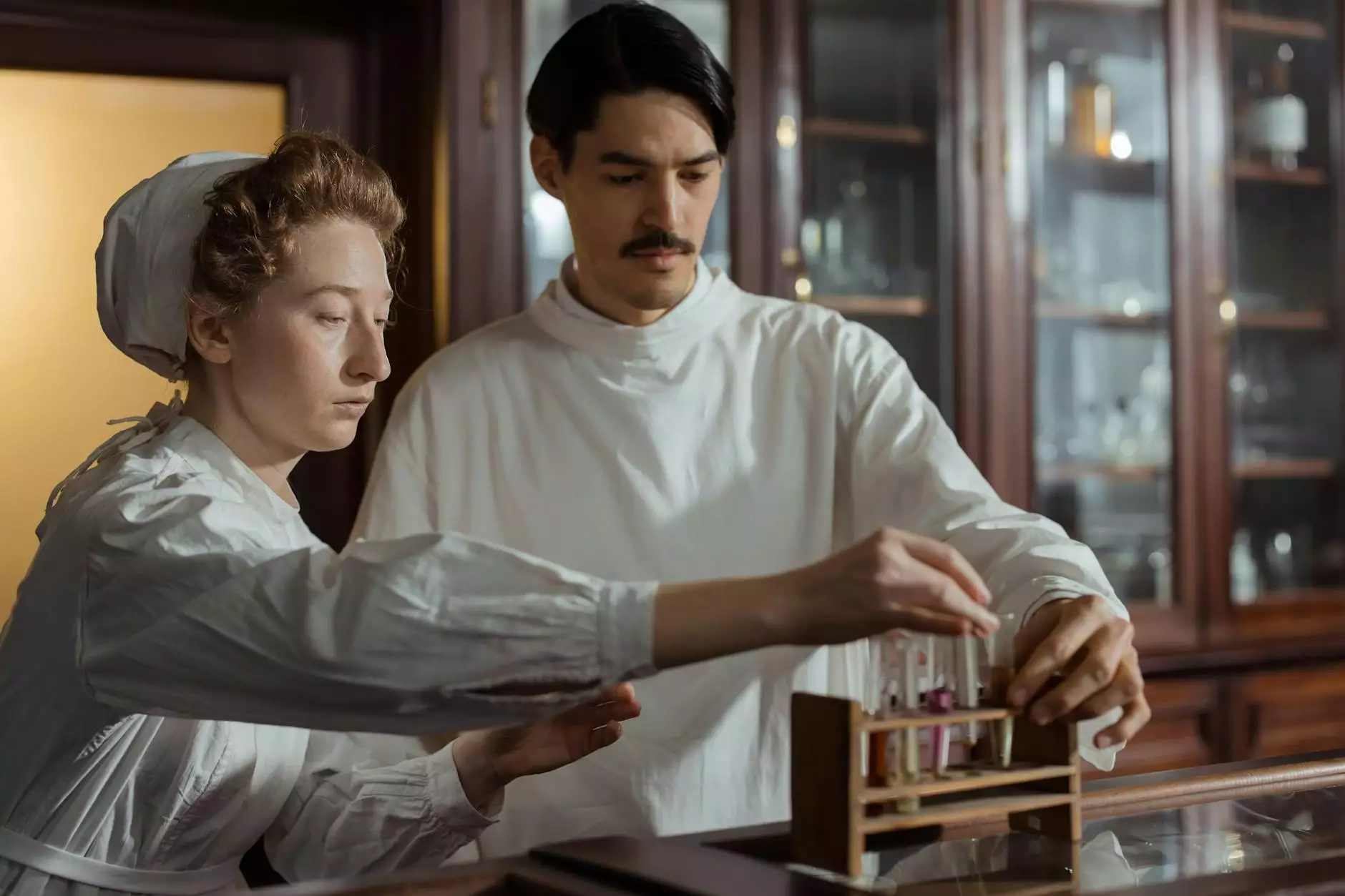
The significance of fume cupboard testing in Newport cannot be underestimated when it comes to maintaining a safe working environment in laboratories and commercial settings. As health and safety regulations continue to evolve, so does the necessity for rigorous assessments of ventilation equipment. This article delves into the various aspects of fume cupboard testing and outlines how businesses can benefit from professional services, particularly in Newport.
Understanding the Importance of Fume Cupboard Testing
Fume cupboards, also known as fume hoods, are critical components in laboratories. They provide a contained environment for handling hazardous substances, ensuring that harmful fumes, vapors, and particles are safely ventilated away from the user. Regular testing of these units is not just a regulatory requirement; it is essential for the protection of laboratory personnel. Below are several reasons why fume cupboard testing is vital:
- Safety Compliance: Adhering to health and safety regulations is mandatory for businesses. Regular testing helps ensure that your fume cupboards meet the required standards.
- Hazard Prevention: The potential risks involved with exposure to chemicals can lead to severe health issues. Testing reduces the chance of accidents and protects employees.
- Equipment Performance: Just like any other equipment, fume cupboards require regular maintenance and testing to ensure they function correctly. This enhances their performance and lifespan.
- Professional Credibility: Companies that prioritize safety demonstrate responsibility. This can enhance your business's credibility and trust with clients and employees.
What Is Involved in Fume Cupboard Testing?
Fume cupboard testing involves a series of assessments to evaluate the performance and safety of the equipment. Here’s a detailed breakdown of the typical testing procedures:
1. Visual Inspection
A qualified technician will conduct a thorough visual inspection of the fume cupboard. This includes checking for:
- Structural integrity
- Condition of seals and gaskets
- Proper placement and functionality of airflow indicators
- Cleanliness and absence of chemical residues
2. Airflow Testing
Ensuring that adequate airflow is maintained is critical. During this phase, the technician will:
- Measure face velocity to ensure it meets manufacturer specifications.
- Assess the airflow pattern within the cupboard to identify any dead spots.
- Utilize smoke tests to visualize airflow dynamics.
3. Performance Testing
The fume cupboard is tested under operational conditions to ascertain its performance. This includes:
- Testing with simulant chemicals to simulate real working conditions.
- Evaluating noise levels associated with the fume cupboard's operation.
- Ensuring that the cupboard can contain spills effectively.
4. Documentation and Reporting
Once testing is complete, detailed reports are generated. This documentation is vital for compliance and should include:
- Test results and findings
- Recommendations for maintenance or repairs
- Certificates of compliance for regulatory purposes
Why Choose Professional Services for Fume Cupboard Testing in Newport?
Choosing a professional service for fume cupboard testing in Newport offers numerous advantages:
1. Expertise and Experience
Professionals possess the necessary qualifications and experience to conduct accurate fume cupboard testing. Their expertise ensures comprehensive assessments and compliance with all regulations. Trusted service providers such as Safe Plant UK ensure that testing is thorough and reliable.
2. Advanced Equipment and Techniques
Professional testers utilize the latest technology and techniques to gather precise data. This includes advanced airflow measurement tools and digital reporting methods, which enhance the accuracy of tests.
3. Peace of Mind
Knowing that a reputable company is overseeing the safety of your laboratory equipment removes the burden from your shoulders. It allows you to focus on your core business activities while ensuring your environment remains safe.
4. Follow-up Support and Services
After testing, professional services often provide additional consultation for necessary follow-up actions, including recommendations for repairs or upgrades. This ensures your fume cupboards remain compliant and efficient.
The Regulatory Landscape for Fume Cupboard Testing
You may wonder what laws and regulations apply to fume cupboard testing in Newport. Understanding these frameworks is crucial for compliance. In the UK, the following regulations apply:
- The Control of Substances Hazardous to Health (COSHH) Regulations: These regulations require employers to ensure that exposure to hazardous substances is properly controlled, which includes proper assessments of fume cupboards.
- Health and Safety at Work Act: This foundational legislation mandates that employers provide a safe working environment for all employees. Regular testing of fume cupboards is integral to fulfilling this obligation.
- Local Authority Guidelines: Local councils often have specific requirements regarding laboratory safety; it is essential to check any local regulations that may apply to your operations.
Best Practices for Maintaining Fume Cupboards
In addition to regular testing, businesses should adopt best practices to maintain their fume cupboards effectively. Here are some critical practices to integrate:
1. Regular Cleaning and Maintenance
Keep fume cupboards clean by regularly removing any chemicals and debris. Establish a schedule for maintenance checks to identify any potential issues before they become significant problems.
2. Staff Training
Ensure that all laboratory staff are adequately trained in the use of fume cupboards. Regular training sessions can help reinforce the importance of safety protocols and proper equipment usage.
3. Monitor Performance Continuously
Implementing ongoing monitoring allows you to track the performance of fume cupboards between testing intervals. This might include regular visual checks and airflow assessments by trained staff.
4. Keep Updated with Regulations
Stay informed about changes in health and safety legislation that may impact your operations. This will ensure your company remains compliant and prepared for future inspections.
Conclusion: The Future of Fume Cupboard Testing in Newport
As businesses in Newport continue to prioritize health and safety, the demand for effective fume cupboard testing will only grow. Engaging with experienced professionals helps ensure that workplaces are not only compliant with regulations but also provide a safe environment for employees. Companies like Safe Plant UK are dedicated to enhancing laboratory safety through thorough testing and unmatched service quality.
Invest in fume cupboard testing today to secure a safer future for your business and its employees.
fume cupboard testing newport